WE2Regal
Active Member
- Joined
- Feb 22, 2003
- Messages
- 429
I think everyone agrees the compressor housing on the '78 to '83 carbed turbo is a terrible design. The 3 bolt flange, commonly referred to as the "foot", that mounts the turbo to the intake manifold, seems to get a lot of the blame for lack of performance. The truth is the entire housing is too small and is flow limted by it's size. But adapting other housings would be very involved with numerous obstacles to overcome to make one work. It can be done and I've been trying to figure out the best way to do it. But for now I'm going to work with a stock housing. You can see in this picture the size difference between the '78-'83 housing, an '84-85 housing and an '86-87 compressor housing.
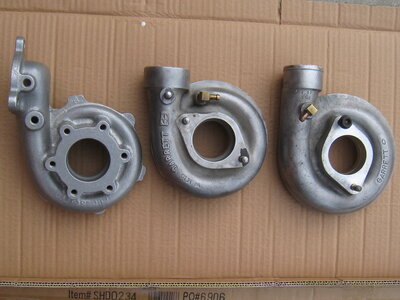
The outlet hole inside the compressor housing going into the 3 bolt flange "foot" area is very small in diameter. Airflow is directed into the middle of the foot through a narrow neck and doesn't take advantage of the 2 inch wide exit hole into the intake manifold. After crashing into the wall of the foot, airflow then has to make a sudden 90 degree turn going down into the intake manifold. The sharp top corner angle of the foot creates more turbulance.
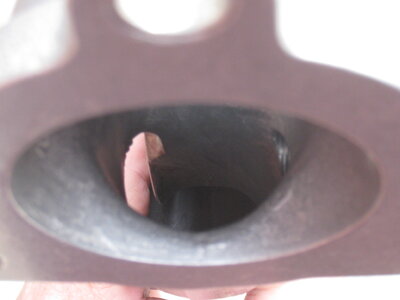
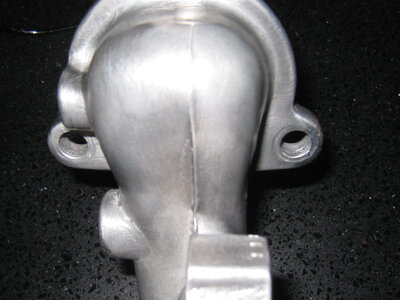
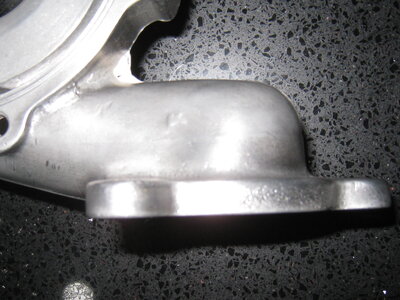
I decided to see if there was any room for improvement by porting the exit of the compressor housing into the mounting flange or "foot" area. In order to really make any flow improvement, the sides of the housing at the neck needed to be welded up so that I could widen the neck without breaking through to the outside. And I DEFINATELY would have.
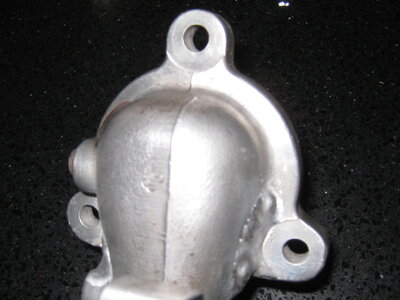
I used 7" long cutters to port the sides wider and also started the downward 90 degree turn downward further up inside the compressor housing. I used one with a rounded nose and one Christmas tree shape to get the areas cut down. It's tedious because you can't see inside while your grinding with the cutter inserted at such a sharp angle. You have to cut a little and then stop to look and feel inside. I've never ported anything that allowed for so much material to be removed! I had aluminum chips everywhere. I followed up with cone shaped sanding rolls to smooth it as best I could. Although you can't see it in the picture, the airflow now starts the 90 degree turn downward about 1 1/2" up inside the housing and the neck is much wider with the airflow having a straighter shot and directed to the entire 2 inch exit hole in the flange. It's not pretty but should be an improvement. Here is a comparison of the ported housing with an untouched housing.
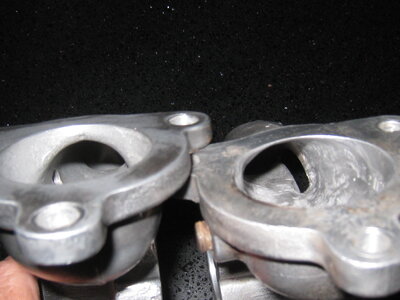
I also filled in the dead space in the upper corner of the foot with Epoxy. This should help direct the airflow downward more smoothly instead of crashing into that sharp corner. I should have done this last because the heat from welding turned it dark colored.
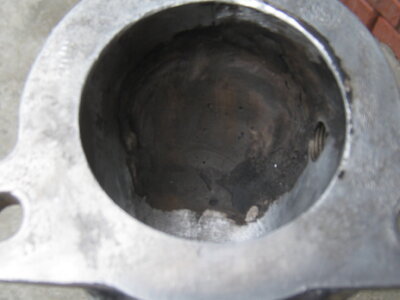
There's room for opening up the hole in the mounting flange also. Laying a gasket on the flange shows it can be made larger and still seal against the intake manifold. Of course the intake manifold itself needs to be opened up the same to match.
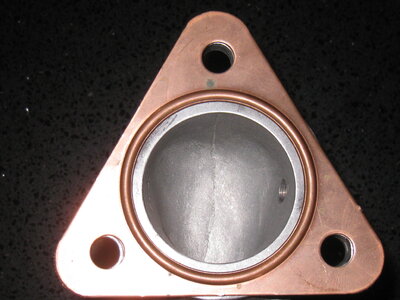
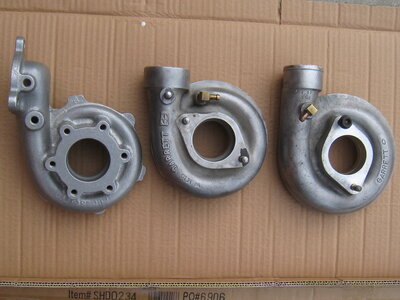
The outlet hole inside the compressor housing going into the 3 bolt flange "foot" area is very small in diameter. Airflow is directed into the middle of the foot through a narrow neck and doesn't take advantage of the 2 inch wide exit hole into the intake manifold. After crashing into the wall of the foot, airflow then has to make a sudden 90 degree turn going down into the intake manifold. The sharp top corner angle of the foot creates more turbulance.
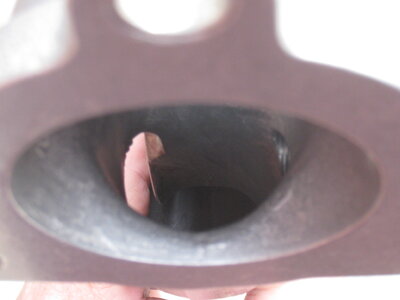
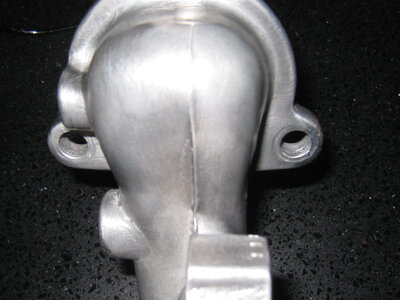
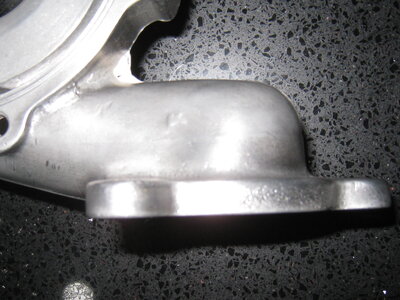
I decided to see if there was any room for improvement by porting the exit of the compressor housing into the mounting flange or "foot" area. In order to really make any flow improvement, the sides of the housing at the neck needed to be welded up so that I could widen the neck without breaking through to the outside. And I DEFINATELY would have.
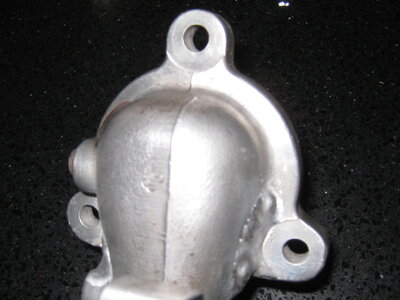
I used 7" long cutters to port the sides wider and also started the downward 90 degree turn downward further up inside the compressor housing. I used one with a rounded nose and one Christmas tree shape to get the areas cut down. It's tedious because you can't see inside while your grinding with the cutter inserted at such a sharp angle. You have to cut a little and then stop to look and feel inside. I've never ported anything that allowed for so much material to be removed! I had aluminum chips everywhere. I followed up with cone shaped sanding rolls to smooth it as best I could. Although you can't see it in the picture, the airflow now starts the 90 degree turn downward about 1 1/2" up inside the housing and the neck is much wider with the airflow having a straighter shot and directed to the entire 2 inch exit hole in the flange. It's not pretty but should be an improvement. Here is a comparison of the ported housing with an untouched housing.
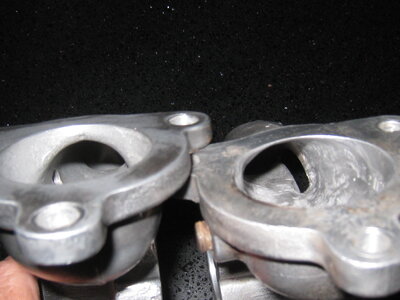
I also filled in the dead space in the upper corner of the foot with Epoxy. This should help direct the airflow downward more smoothly instead of crashing into that sharp corner. I should have done this last because the heat from welding turned it dark colored.
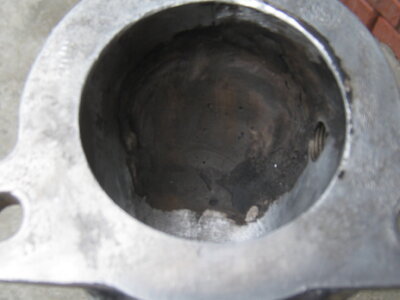
There's room for opening up the hole in the mounting flange also. Laying a gasket on the flange shows it can be made larger and still seal against the intake manifold. Of course the intake manifold itself needs to be opened up the same to match.
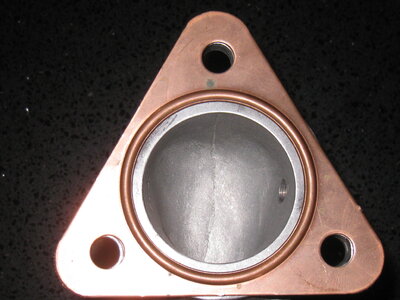