Drewster
Wish I Had A Clone. AKA Andrew Youlio
- Joined
- May 31, 2001
- Messages
- 787
I’m thinking the #2 oil feed hole is way to small on the Clevite MS-960P set. Im planning on drilling it out to match the other holes unless someone has a good reason to leave as is. See pics, compare and comment please.
Gona go tighten caps and bore gage clearance now. Going to do new bearings and clean up crank.
Sent from my iPhone using Tapatalk
Gona go tighten caps and bore gage clearance now. Going to do new bearings and clean up crank.
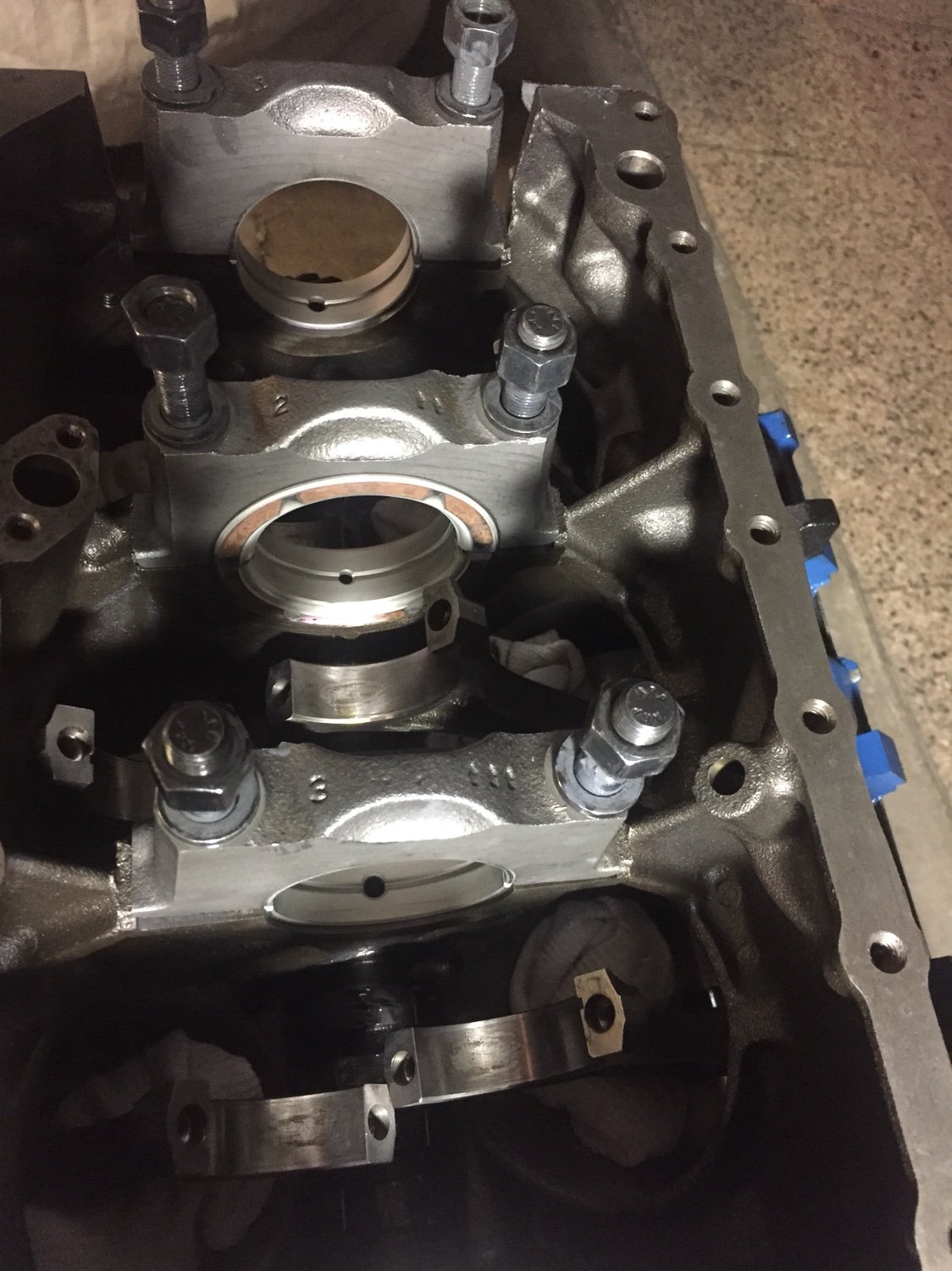
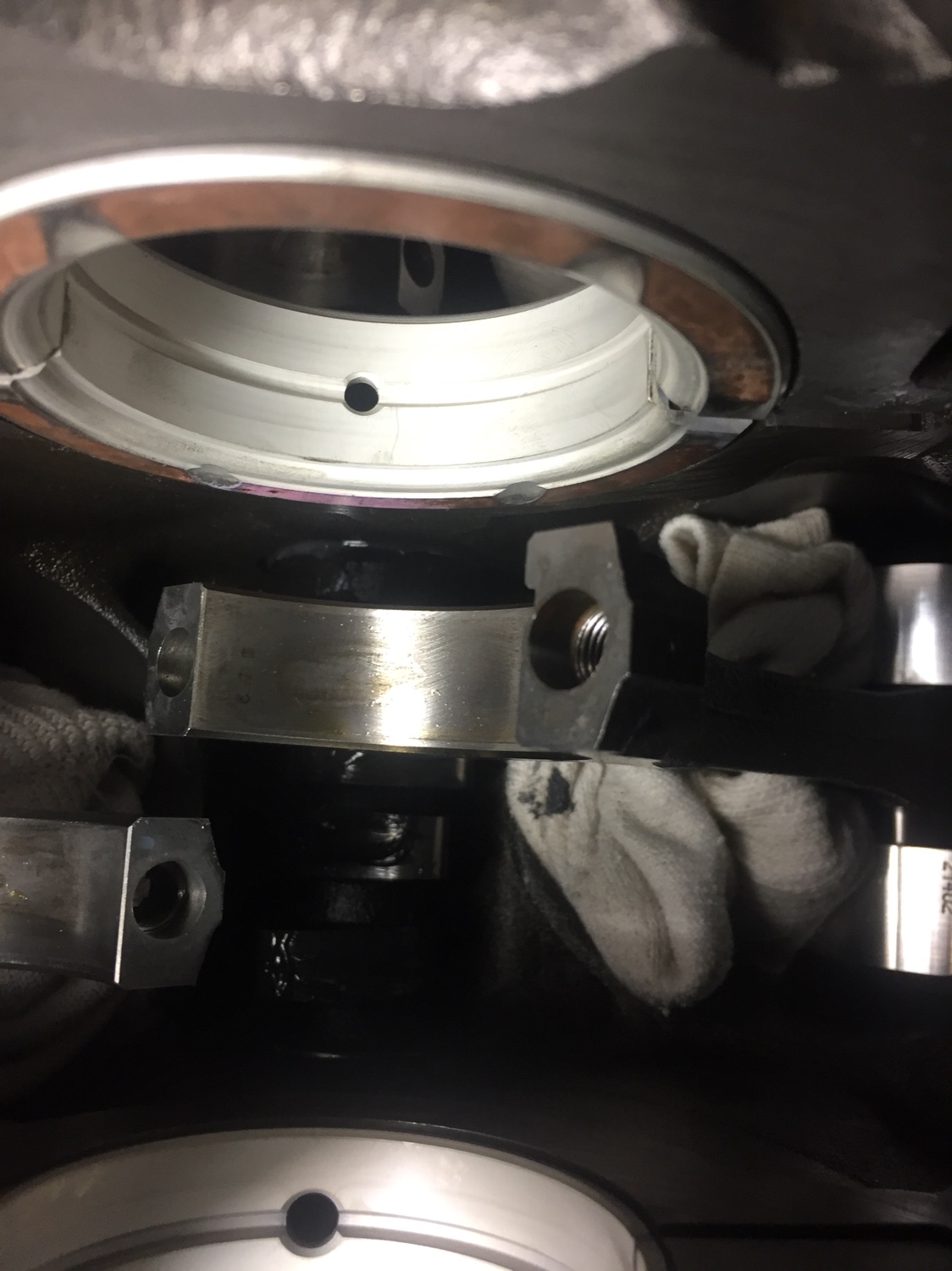
Sent from my iPhone using Tapatalk